
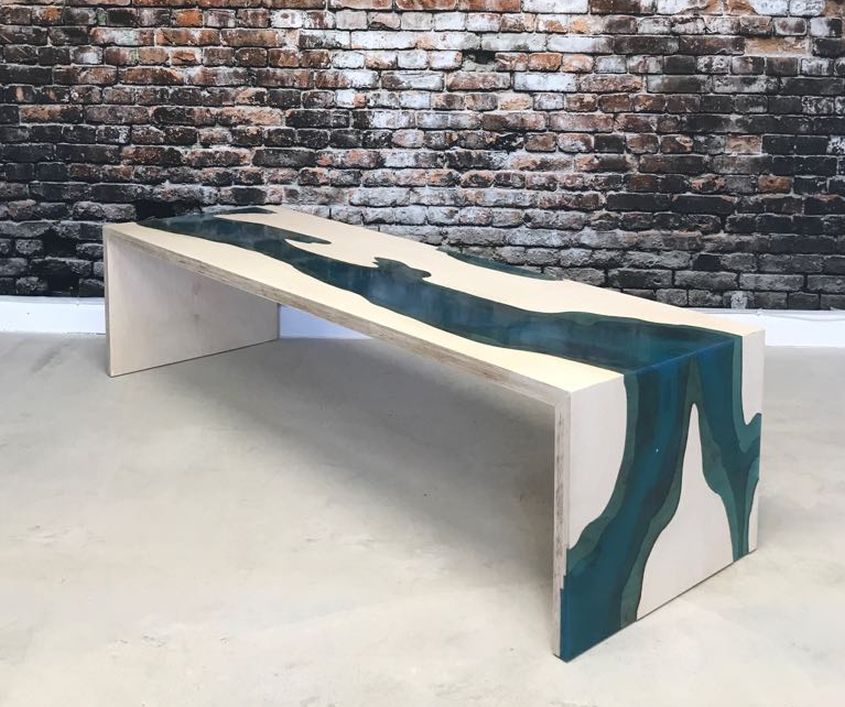
I drilled mounting holes in the base for the top, then I primed it and sprayed on some matte black paint and matte clear coat. It was nice to have a cordless grinder so I could grind in the side yard and keep the metal dust out of the shop. Thanks to Lincoln Electric for having me out and to Doug from RetroWeld and John Malecki for helping with the base and filming.īack home I ground down the welds on the base with my cordless grinder and a flap disc. I’m really excited to do more welding projects in the future. I used the Lincoln MP210 to weld together the base, and it was quick to learn with the digital readout. While I was there I went to a local metal shop and picked up some 1” square tube for the base. I was the newbie of the bunch and learned the basics of MIG and TIG welding.
#Waterfall coffee table wood diy how to
They brought a group of YouTubers and local makers together to teach us how to weld better. While the epoxy was curing I actually flew to Cleveland for the Spring Make event with Lincoln Electric. The colors mixed together and it turned out amazing. Now I wouldn’t necessarily recommend this, but it worked for me. After some thought I decided pour the ends at the same time using both hands. I had to figure out how to pour epoxy resin with two colors to get a good mix. The deep blue and the green turned out awesome and the silver pearlescent gave it some extra depth. I added some metallic pigment to the epoxy resin and stirred each mix for several minutes. I wanted a two-color pour so I measured out 1.5L of the 2 to 1 mix in one container and 1L in the other. Here is another cheaper epoxy resin alternative, but you will have to pour multiple thinner coats to keep it from cracking. That specific resin will let you pour up to 1-3/4″ at a time. I used an epoxy resin with a 2 to 1 resin to hardener mix. Then I added up all those numbers and multiplied by the height of the slab to get the total volume of the gap. I measured the gap between the slabs in 4 to 8” segments at a time and multiplied the average gap by the length of that segment. Next I figured out how much epoxy resin I needed for my epoxy resin table DIY pour. Pour Epoxy Resin into the River Table Form The form needs to be level for the epoxy pour so I shimmed up one end of my bench to even things out. I also used hot glue to seal some small gaps at the end of the slabs to keep the epoxy out. You could also just clamp them down if you don’t want holes in the underside. To keep the slabs from floating on the epoxy resin, I clamped the wood down and screwed it to the form from underneath.
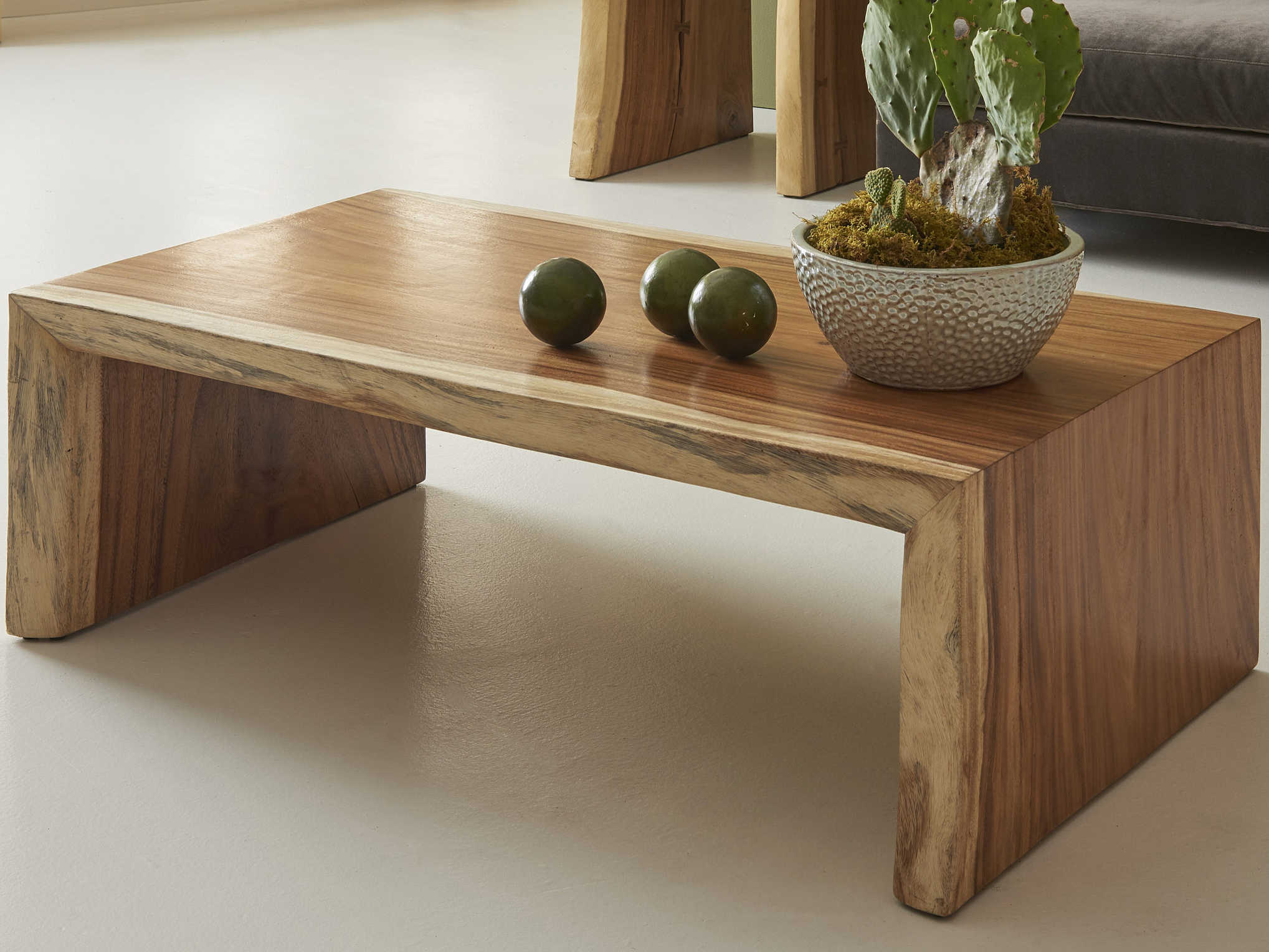
I loaded the live edge slabs into the form and could really see the shape coming together. If I do it again I’ll probably use silicone to seal the corners as the taping took quite a while, especially in the 3-way corners. I put the epoxy resin form together with screws and then sealed the inside corners of the form with more sealant tape. To keep the epoxy resin from sticking to the form I covered the pieces in a sealant tape. I used ¾” MDF for the form but plywood or melamine can also be used here. While the epoxy was setting up I moved on to making the form for the pour. This will help stabilize the edge and keep the epoxy from leaking out during the pour. I taped up the bottom of the cracks then mixed up some 5 minute epoxy to fill the voids. The slabs were pretty gnarly and had some good size checks and cracks in them. I sanded off any loose material and got a good surface for the epoxy to stick to. To prep for the epoxy resin pour I needed to clean up the live edges. The slabs were too thick and long for the DIY epoxy river table design I was going for, so I machined then down to the right thickness then cut them to size on my miter saw. I surfaced the slabs flat on one side with my jointer, then used that reference face to flatten the other side with my planer. With the live edge slab cut into two halves I took them through a few milling operations to get the boards ready for the next step. The cherry slab was just a little thicker than the depth of my blade so I had to finish off the cut the old fashioned way by hand. I clamped a straight edge to the live edge slab and used my cordless circular saw to cut the slab in multiple passes. Then I played around until I found the line I wanted and marked both ends for the cut. To find the best cut line, I used a string and centered it on each end of the slab. I was given this old cherry slab a few years ago and when I started planning for this project I knew it was the perfect piece to rip in half to give me a DIY river table. How to Make a DIY Epoxy Resin River Table
